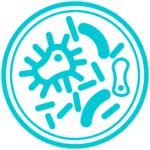
Knowledge
Identify the microbial actors and pathways, chemical species, and
MIC mechanisms that lead to facility failures
In this activity, our team is working on 5 major objectives to better understand MIC in various oil and gas operations:
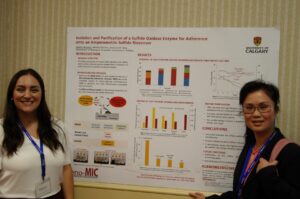
- Developing standard operating conditions for sampling, preservation, and genomics analysis (e.g., DNA extraction, PCR methods) for field samples related to MIC (view SOPS)
- Building a microbial corrosion database (genomic and chemical) and an MIC ontology
- Understanding MIC in offshore oil recovery operations (topsides) by:
- Determining the key chemical environments that favor MIC (e.g., identifying key N and S compounds)
- Identifying the key microbial processes (e.g., related to N and S biotransformations) occurring within topside infrastructure that may lead to MIC
- Assessing the microbial communities and chemical interactions that lead to MIC in onshore operations including upstream, midstream, and transmission pipelines; for example, how does under deposit corrosion occur?
- Identifying biocide resistance genes within corrosive microbial communities in oil and gas infrastructure
Learn more about individual projects with in this theme
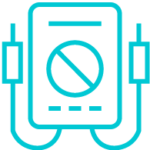
Assays & Devices
Develop omics- and chemical-based monitoring tools to detect and measure MIC and associated chemical end-products
Our team is developing -omics and chemical-based monitoring tools for detecting MIC through the following 3 major objectives:
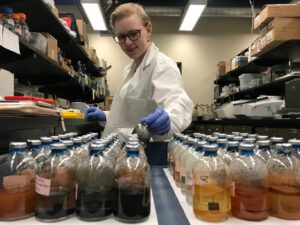
- Determining comprehensive omics-based primer sets and rapid PCR assays (e.g., via ‘lab-on-chip’ devices) to identify key genes associated with MIC for improved monitoring of field samples
- Building and assessing new in-line pipeline corrosion and biofilm monitoring systems that will pinpoint problematic areas due to microbial growth within pipeline systems
- Developing chemical and biological sensors is order to assess operations for ‘leading’ chemical indicators that MIC may be a problem via:
- Creation of new molecular imprinted polymers (MIPs) for chemical detection
- Development of a biosensor specific for sulfide detection
Learn more about individual projects with in this theme
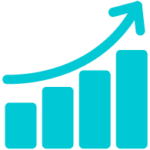
PREDICTIVE & RISK MODELS
Devise better predictive modeling and risk assessment tools
As modeling is a key tool used by the oil and gas industry to help predict corrosion and assess risk, this objective aims to build predictive and risk assessment models that incorporate biological factors (as determined in this project) that will be easily incorporated into models already used by industry through the following 3 major objectives:
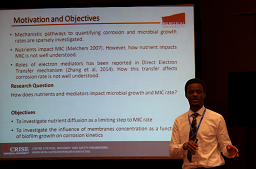
- Building and improving MIC mechanistic and predictive models through:
- Modelling corrosion at the molecular level
- Developing one or more predictive MIC corrosion models
- Building and improving MIC mechanistic and predictive models through:
- Modelling corrosion at the molecular level
- Developing one or more predictive MIC corrosion models
- Developing MIC risk assessment models in oil and gas operations through:
- Fitness for service (FFS) assessments
- Risk-based integrity management (RBIM) methodology
Learn more about individual projects with in this theme
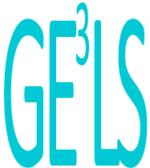
KNOWLEDGE TRANSLATION
Improve corrosion control strategies to reduce potential failures
In the discovery of knowledge that has potential practical applications, it is of upmost importance to relay this information to industry for actual uptake and use. This GE3LS component focuses on how best to translate and apply the knowledge gained in this project to MIC monitoring, detection, and control through the following 3 major objectives:
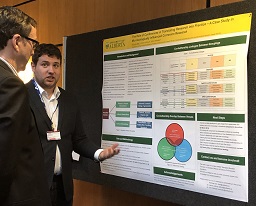
- Identifying the barriers for knowledge translation through:
- Bibliometrics – an examination of where information is presented by various stakeholders (where does academia vs. industry present information?) to determine where gaps exist in communication of information so that these can be overcome
- Surveys of stakeholders (e.g., oil and gas companies, service companies, regulators, consultants, public) to assess how/why/where new information is obtained
- Developing new recommended guidelines for MIC detection and monitoring that can be integrated into existing corrosion management frameworks through:
- Preparing ‘Recommended Guidelines’ for detection, quantification, and mitigation of MIC for:
- Integrating into known standard organizations (e.g., into NACE, DNV-GL, ASTM standards)
- Building a ‘MIC Failure Analysis Protocol’ that guides industry towards forensic methodologies specific to identifying MIC as part of failure analysis protocols
- Preparing ‘Recommended Guidelines’ for detection, quantification, and mitigation of MIC for:
- Ensuring effective dissemination methods of knowledge (e.g., communications in appropriate journals/trade magazines, academic vs. industry conferences) and evaluation of impact